Esco BioVap™ BSC Bio-decontamination System
Hydrogen Peroxide (H2O2)
Hydrogen peroxide (H2O2) is widely used as a biocide, mostly on kind of application where its non-toxic by-products is significant. The use of hydrogen peroxide has the following main advantages: broad-spectrum activity including its efficacy against bacterial endospores, lack of environmental toxicity following their complete degradation. H2O2 is particularly interesting for its application in liquid but also vaporized form for antisepsis and for the disinfection of surfaces and medical devices and for room fumigation.
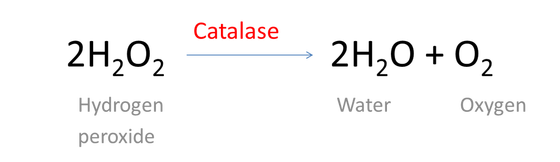
Source: http://brilliantbiologystudent.weebly.com/effect-of-temperature.html
H2O2 Biocidal Effect
The hydrogen peroxide molecule has a unique geometry with a high-energy angle, which makes splitting of O-O-bond easy.
The biocidal effect of hydrogen peroxide comes from the oxygen atom/radical, which is released under influence of the enzyme catalase at the microbial surface. The oxidative power of oxygen radicals cause irreversible damage to enzymatic systems and microbial DNA.
BioVap™ Development
Esco have been looking for an alternative cost effective bio-decontamination system.
The use of conventional Hydrogen Peroxide Vapour (HPV) gaseous bio-decontamination systems have been used within the pharmaceutical industry and Healthcare industries for many years. These systems without a doubt have established that Hydrogen Peroxide is a highly efficient Sterilent that decomposes to just oxygen and water, leaving no lasting oxidizer on any surfaces
Esco pursued a bio-decontamination system that could rival these well-established systems with regards to efficacy, cleanliness and overall performance for repeatable bio-decontamination cycles to provide a log 6 (10-6) reduction in bio-burden, validated using biological indicators populated with Geobacillus stearothermophilus spores.
Consideration of using a fogging system was investigated as these systems were becoming more popular with cleanroom and/or laboratory bio-decontamination, but to date, there are no strong moves to retrofitting this technology to barrier technology. The principle of these systems is that Sterilent is forced through a nozzle under pressure and thus atomizes the Sterilent into micron size particles to produce a dry fog. Physics defines dry fog and refers to droplets that average <10micron diameter in size.
Figure 1. Size of particles under different atomization
Atomizing to small particles would be good for the distribution of the Sterilant however at small particle sizes, the droplets would take a long time to settle on surfaces to be sterilized and thus return long bio-decontamination cycles. It was discovered that with this new system, the sterilant remains as a liquid, unaffected by temperature or humidity therefore no conditioning phase is required to pre-condition the barrier system.
Conventional Gaseous Systems
Pre-conditioning | Gassing / Injection | Dwell | Aeration |
Esco BioVap™ System
Gassing / Injection | Dwell | Aeration |
Esco BioVap™ System, works on the principle of vaporising the sterilant as it is injected into the chamber through a fine Ultrasonic atomiser nozzle. The atomized droplets are made up of different reactive molecular species within a water matrix. Each atomized particle contains billions of reactive molecules. When these droplet contact the surfaces they immediately start the bio-decontamination process.
BioVap™ Bio-decontamination System
The BioVap™ system is PLC controlled with operator interface via a touch screen HMI terminal giving operator log on security and real time display of cycle parameters. Cycle parameters are also recorded and a printout of the cycle parameters is given at the end of a cycle for validation records.
As programmed by Trained Esco NSF Service Engineer:
Cycle No. | Injection time | Dwelling Phase | Aeration Time |
1 | 10 minutes | 10 minutes | 1 minute |
2 | 15 minutes | 10 minutes | 1 minute |
3 | 20 minutes | 10 minutes | 1 minute |
PROCEDURE:
The BioVap™ bio-decontamination cycle will have the following phases:
a. Injection Phase – In this phase the sterilant will be injected into the space as a dry fog at a set pressure and set flow rate for a set period of time, during this period the atomizing pressure, the injection airflow and injection air pressure are monitored.
b. Dwell Phase - In this phase the sterilant is allowed to settle on the surfaces inside the space for a set period of time and affect the microbial kill.
c. Aeration Phase - In this phase the hydrogen peroxide sterilant is removed from the space / enclosure.
Fumigation Testing:
The fumigation is done in EC2-4L8 Class II Cabinet. Pre-filter in paper catch is removed and exhaust and supply blower speed are both adjusted to 20% of nominal set point before fumigation starts.
Biological indicators were placed to monitor the fumigation process. See photos below, BI location inside the plenum.
Biological indicators were placed to monitor the fumigation process. See photos below, BI location inside the work zone.
The time required to carry out BioVap decontamination is outlined below for cycle #1:
No. | Process | Time |
1 | Set-up & sealing the front aperture of BSC | 45 minutes |
2 | Injection Time | 10 minutes |
3 | Dwelling Time | 10 minutes |
4 | Aeration Time | 1 minute |
5 | Tear-down & cleaning the BSC (substantial) residue | 15 minutes |
Total time required to carry out BioVap decontamination | 81 minutes |
Note: Nozzle was manually adjusted enough to produce mist and not create too much condensation inside the cabinet work zone.
Decontamination Sealing Method:
- Put the BioVap nozzle assembly inside the cabinet then seal open areas. Use the 50 mm wide tape to seal the gap between the plastic sheet and the sash glass. To compensate for areas where the plastic must turn, use multi section tape. Ensure that the two layers of tape overlap at the end points to prevent leakage. As shown in the photo below:
- Connect the nozzle to Mobile BioVapTM System.
- Connect the compressor to Mobile BioVapTM System.
Note: Make sure all connector are fitted correctly. And no leak on H2O2 line from Mobile BioVapTM System to nozzle. A small leak will resulted to unsuccessful process.
- Load the H2O2 bottle to BioVap equipment.
- The BSC is ready for H2O2 decontamination.
Injection Cycle
After 3 minutes of injection time from the beginning, a lot of fog must observed (equally visible in all corner) inside the work zone, ON the blower for 10-15 seconds. You will observe the fog becomes thin, then OFF the blower. I repeat it twice during the 10 minutes of injection time.
Dwelling Phase
Sterilant is allowed to settle on the surfaces inside the space for 10 minutes.
Aeration Time
On the blower for 1 minute to remove from the space the hydrogen peroxides sterilant.
Results:
Cycle # | Remarks | BI Results |
1 |
1st = Top Note: BI turns negative when the pre-filter on paper catch removed and centre tray also removed. Several running was unsuccessful when pre-filter was there even a lot of fog. I did not notice that this cabinet have this kind of filter in paper catch. (One of the factor to be consider, when BI turn to positive). 10 minutes injection time |
![]() |
1 |
2nd = 1st = Top (Supply Filter) Note: For EC2-4E8, BI turns negative. All trays are installed and no pre-filter in paper catch. Blower adjusted to 20% of Nominal. 10 minutes injection time |
![]() |
2 |
1st = Top (Supply Filter) Note: BI turns negative. Only centre tray remove and no pre-filter in paper catch. Blower adjusted to 50% of Nominal. 10 minutes injection time |
![]() |
2 |
1st = Bottom (Exhaust Filter) Note: BI turns negative. All trays are installed and no pre-filter in paper catch. Blower adjusted to 20% of Nominal. 15 minutes injection time |
![]() |
3 |
1st = Top (Supply Filter) Note: BI turns negative. All trays are installed and no pre-filter in paper catch. Blower adjusted to 20% of Nominal. 10 minutes injection time |
![]() |
Note: Results between 10 and 15 minutes injection time, 20% and 50% blower cycle are the same.
Factors to be consider when fumigation process is not successful.
- If the fog is very thin inside the work zone during injection time.
- Pre-filter on paper catch.
- Leak on H2O2 line from BioVap to nozzle.
Esco BioVap™ System Implementation
Esco BioVap™ system is developed to be flexible enough to adapt to different requirements of customers and facilities, from cabinets and transfer hatches up to modular enclosures to isolators.
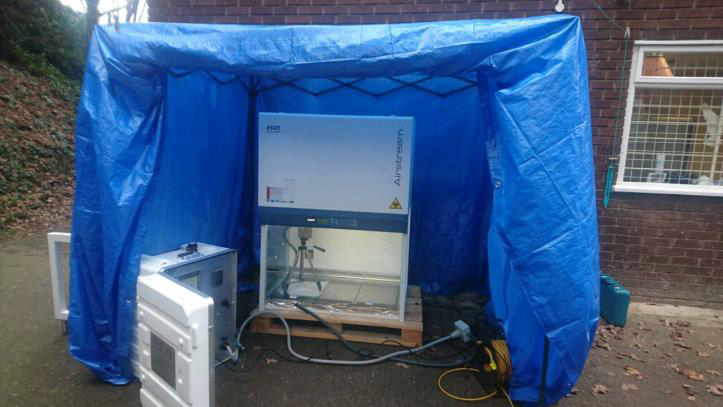
Esco has successfully provided the BioVap™ Bio-decontamination System to the laboratories of the following companies in UK:
- Chemopet, Chemopet LLP, The health Business & Technical Park, Runcorn, Cheshire
- Pall Manufacturing, 5 Harbourgate Business Park, Southampton Road, Portsmouth
- Quintiles Drug Research, Quintiles Drug Research Unit, Pharmacy Department, 6 Newcomen Street, London
- University of Manchester, Scalpel Lab, Floor 2, Wolfson Molecular Imagaing Centre, 27 Palatine Road, Manchester
- Gowrie Ltd., Unit 4 Bradfield Road, Ruislip, London, Middlesex
Esco BioVap™ Bio-decontamination Video
References:
- Ezra Linley, Stephen P. Denyer, Gerald McDonnell, Claire Simons, Jean-Yves Maillard; Use of hydrogen peroxide as a biocide: new consideration of its mechanisms of biocidal action. J Antimicrob Chemother 2012; 67 (7): 1589-1596. doi: 10.1093/jac/dks129
- Esco Pharma. How Clean is Clean Enough?: BioVap™ Bio-decontamination System.
Available from: http://www.escopharma.com/news/61/