Optimizing Safety: BSC Installation and Maintenance Best Practices

Biological Safety Cabinet Overview
A Biological Safety Cabinet (BSC) is a specialized type of enclosure commonly employed within laboratory settings to safeguard laboratory personnel from potential exposure to hazardous substances. This cabinet operates on a principle of controlled airflow, creating a barrier between the laboratory environment and any samples or materials that might carry biological, chemical, or other risks.
The primary purpose of a BSC is to provide a controlled and contained workspace where procedures involving potentially harmful materials can be carried out safely. The cabinet's design includes high-efficiency particulate air (HEPA or ULPA) filters that purify the incoming air and exhaust air, effectively removing any airborne contaminants. This filtration system ensures that any harmful particles generated during experiments or manipulations are trapped and prevented from escaping into the laboratory environment.
There are different classes of BSC, each offering varying levels of protection based on their design and airflow configurations. Each BSC class is designed to meet specific containment needs and is subject to stringent testing and certification to ensure it operates effectively. The airflow patterns are carefully engineered to minimize the risk of cross-contamination and protect both the laboratory personnel and the work being conducted within the cabinet.
Choosing the right class depends on the type of materials being handled, the level of risk, and the laboratory's safety protocols. Here's a brief discussion of BSC classes:
Photo | Purpose | Airflow | Use | |
---|---|---|---|---|
Class I BSC | ![]() AC1-E |
personnel and environmental protection but offer no product protection | unidirectional airflow, with air drawn from the laboratory into the cabinet and then passed through a HEPA filter before being exhausted | for working with low to moderate-risk biological agents |
Class II BSC (3 Types)
|
![]() LA2-S G4 |
provide both personnel and environmental protection, along with product protection | laminar airflow, with a portion of the air recirculated within the cabinet and the rest exhausted after HEPA filtration (Type A, B1) or with 100% exhaust system (Type B2) | ideal for work involving pathogens that require containment |
Class III BSC | ![]() AC3-4B |
highest level of containment and protection | total containment with airtight, gas-tight construction. All operations are conducted through glove ports | designed for work with highly infectious and hazardous agents. |
Biosafety cabinets can also be categorized as ducted (connected to an external exhaust system) or ductless (using internal filtration) based on how they handle airflow and contamination. Ducted cabinets vent air outside, providing maximum containment, while ductless cabinets filter and recirculate air, offering versatility and cost-effectiveness for lower-risk applications.
Ducted BSC
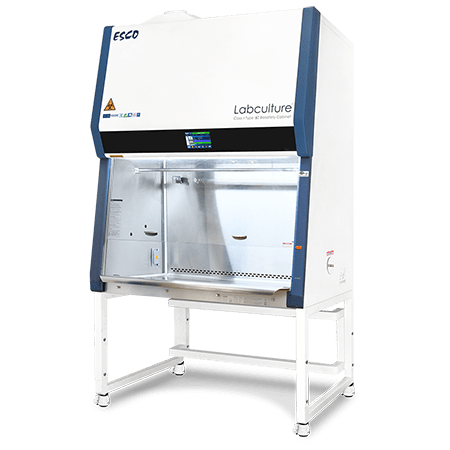
LB2-B G4
Ductless BSC
-min.png)
AC2-S-NS G4
Biosafety cabinets are commonly used in microbiology, immunology, pharmaceutical research, and other scientific disciplines where working with potentially infectious agents, toxic chemicals, or delicate samples is a routine part of laboratory work. By maintaining a contained and controlled environment, these cabinets play a critical role in ensuring the safety of researchers, preventing the accidental release of hazardous agents, and safeguarding the integrity of scientific experiments.
Esco Lifesciences is a leading laboratory manufacturer of biological safety cabinets, providing an extensive range of options across different classes, types, and applications.
Installation Guidelines for Biosafety Cabinets
Biosafety cabinet installation is crucial for safety and effectiveness. It ensures BSCs work properly, meet regulations, and prevent contamination. Proper installation reduces risks and extends BSC life, while also facilitating training and documentation for compliance.
Location Requirements
Location requirements for a BSC are critical to ensure its proper operation and safety. These requirements prioritize maintaining proper airflow, preventing disturbances, and optimizing the working environment for personnel. Consulting experts can help make informed decisions regarding placement for the best possible outcomes.
- Never place cabinets in line with doors, openable windows, or busy paths. Also, consider how room devices like diffusers, fans, extractors, and vents might affect the BSC, and address any airflow issues before installing.
- The cabinet should be placed as far away as possible from sources of airflow disturbance and positioned away from any external airflow disturbances.
- Keep room air supply diffusers at least 1.5 meters (5 feet) away from the cabinet's front opening. If needed near a BSC, ensure low discharge velocity.
- Position the BSC to meet operator and nearby workers' spatial needs for vision, lighting, and access. If it's on a benchtop, align the front with the bench's edge.
- Avoid gaps between the cabinet's front edge and the bench to prevent turbulence and airflow disruption.
- The armrest can be removed to reduce the overall depth of the cabinet if necessary.
- Proper cabinet placement is vital for performance; consult facility engineers and safety experts before installation.
Position Requirements (Based on NSF/ ANSI 49: 2022)
- Clearance from adjacent walls or columns (typically 6 inches or 150 mm).
- Space between multiple BSCs (again, around 6 inches or 150 mm).
- Adequate space, typically 6 inches or 150 mm, should be maintained behind and on both sides of the cabinet to allow for service access.
- A minimum of 40 inches (1020 mm) of open space in front of the BSC for user comfort and safety.
- Proper distance (usually 60 inches or 1520 mm) from opposing walls, benchtops, and areas with occasional traffic.
- Approximately 20 inches (510 mm) between the BSC and benchtops along perpendicular walls.
- A substantial distance (typically 100 inches or 2540 mm) between two BSCs that face each other.
- Adequate space (typically 60 inches or 1520 mm) away from the rear of a doorway.
- A minimum of 40 inches (1020 mm) from the adjacent swing side of a doorway.
- Clearance of about 6 inches (150 mm) from the hinge side of an adjacent doorway.
- For BSCs without exhaust systems, 12 inches (300 mm) clearance is required from the filter face and overhead obstructions in their final operating position. It is important for:
- Exhaust HEPA/ULPA filter testing
- Thermal anemometer use in cabinet inflow calculations
Environmental Requirements
- For indoor use only.
- Suitable for altitudes up to 2,000 meters (6,600 feet); higher altitudes might require airflow sensor calibration.
- Keep relative humidity between 20% and 90%.
- Operate at temperatures ranging from 5°C to 35°C (41°F to 95°F).
- Pollution Degree 2.0
Exhaust Requirements
- The exhaust filter area is sensitive to air currents or drafts.
- Maintain a 30 cm (1-foot) clearance between the cabinet's highest point and the ceiling.
- If the clearance is less than 30 cm, consider recalibrating the airflow alarm system.
- For effective exhaust filter leak scanning, aim for a minimum 50 cm (1-foot 8-inch) clearance.
Best Practices for BSC Operation
BSC usage tips and reminders are essential for maintaining a safe, compliant, and efficient laboratory environment. They safeguard personnel, samples, equipment, and data while ensuring the quality and reliability of research and diagnostic processes. Adhering to these practices is a fundamental responsibility in any laboratory setting.


Biosafety Cabinet Maintenance
a. Scheduled Maintenance
Regular maintenance is necessary for the Biological Safety Cabinet’s trouble-free performance. Stay on track and take note of the checklist below.
Table 1. Scheduled Maintenance Checklist
No. | Description of Task to Perform | Maintenance to be carried out every | ||||
---|---|---|---|---|---|---|
Daily | Weekly | Monthly | Quarterly | Yearly | ||
1 | Surface decontaminate the work zone and LCD Screen | ✔ | ||||
2 | Cabinet power-up alarm verification | ✔ | ||||
3 | Perform thorough surface decontamination on the drain pan | ✔ | ||||
4 | Check the paper catch for retained materials | ✔ | ||||
5 | Clean UV lamp (where present) of any dust and dirt | ✔ | ||||
6 | Clean the exterior surfaces of the cabinet | ✔ | ||||
7 | Clean the sash exterior window | ✔ | ||||
8 | Check all service fixtures (where present) for proper operation | ✔ | ||||
9 | Inspect the cabinet for any physical defects or malfunction | ✔ | ||||
10 | Clean stubborn residue on stainless steel surfaces with stainless steel polisher (Autosol®) | ✔ | ||||
11 | Recertification and check the cabinet's functionality | ✔ | ||||
12 | Change UV Lamp (where present) | Tentatively |
b. Certification
Certification of cabinets, particularly Biosafety Cabinets, is a fundamental practice in laboratory safety. It involves conducting a thorough assessment of the cabinet's performance to reduce the risk of unexpected malfunctions that could compromise user safety and the integrity of experiments or processes.
Esco Lifesciences conducts the following BSC performance testing to ensure they meet global standards for performance, safety, and compliance, reflecting commitment to quality and safety in labs and research.
- Inflow velocity test measures the inlet volumetric flow rate on the front aperture at nominal operating speed.
- Downflow velocity test measures the movement of air out of the cabinet and determines the performance of the blower.
- Particle count test determines air quality by counting and sizing the number of particles in the air and classifying the cleanliness level in a controlled environment.
- Filter integrity test verifies the continued efficiency of the filter by introducing particulates and measuring the output.
- Light intensity test determines light intensity from fluorescent/LED lamp in front to back centerline work surface level of the cabinet.
- Noise level* test determines noise level of the cabinet during normal operation in front of the work surface area lower edge and above the recessed work surface area.
- UV intensity* test determines the light intensity from UV lamp in front to back centerline work surface level of the cabinet.
*Note: This test is optional for field testing.
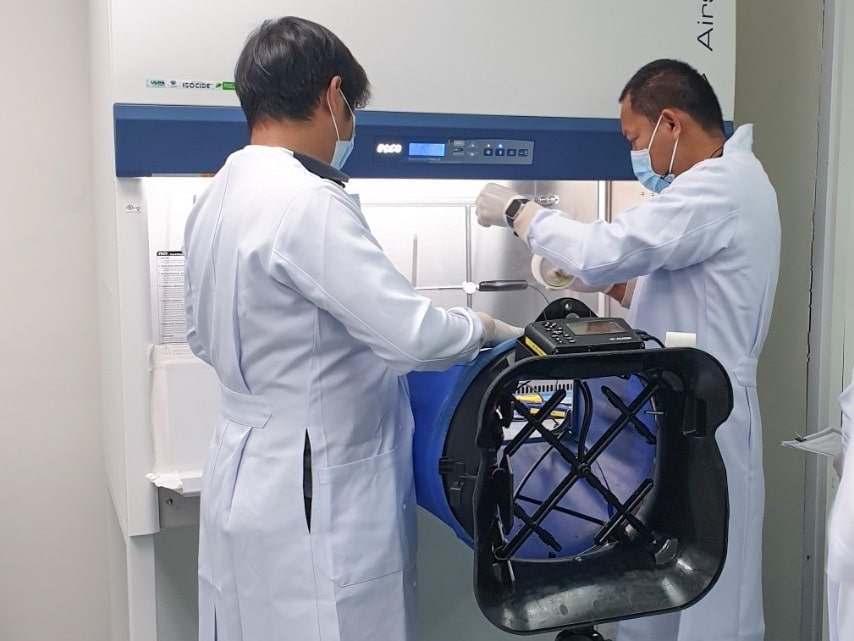
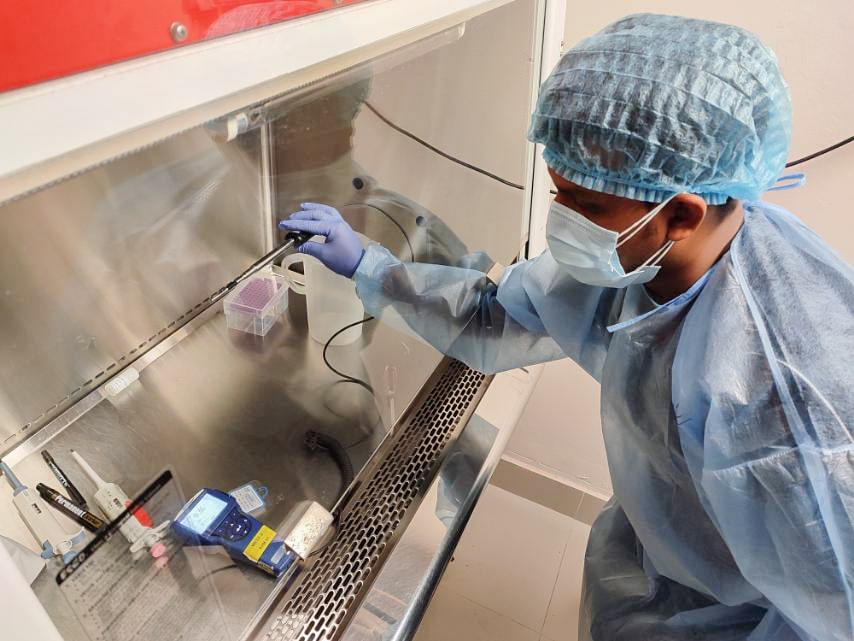
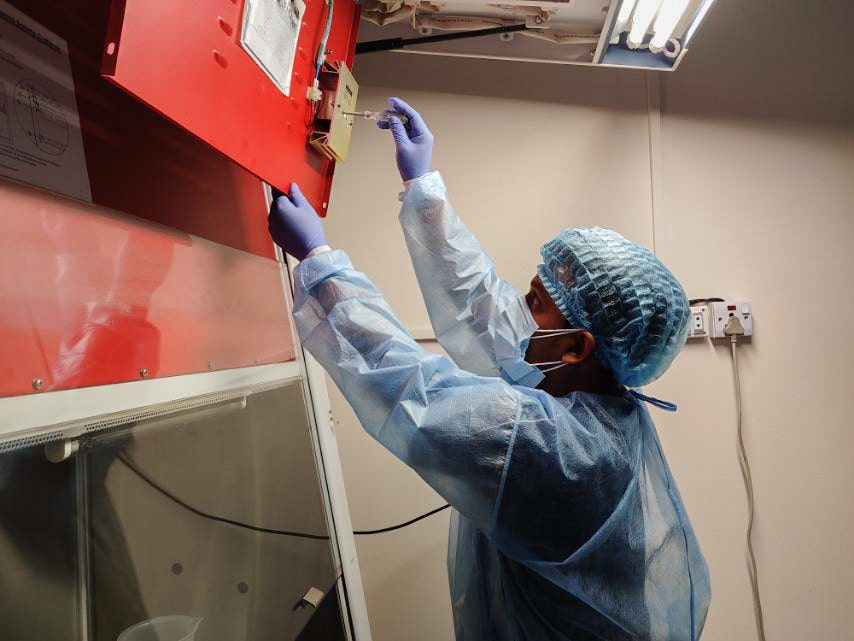
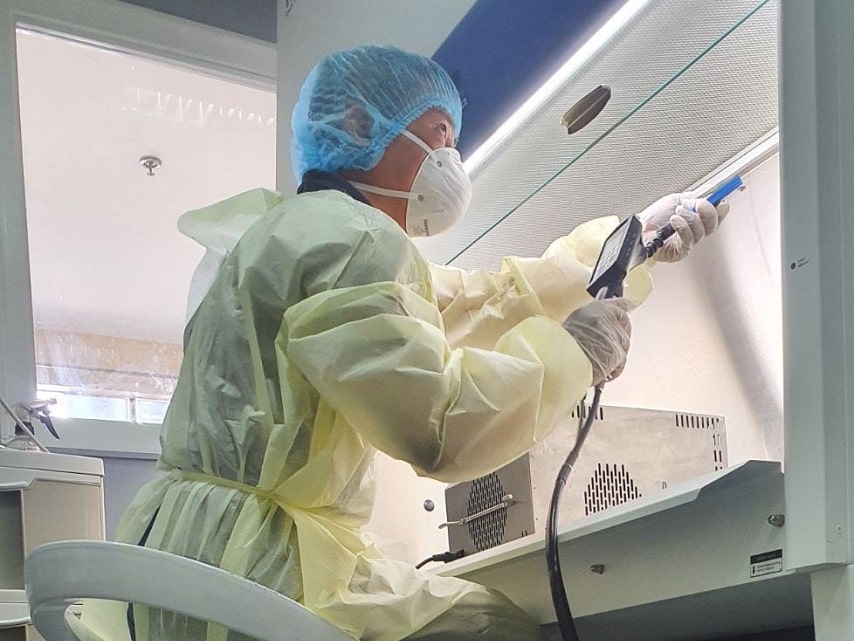
Esco Lifesciences BSC Field Certifiers conducting Biosafety Cabinet performance testing.
c. Cleaning Procedure
- Clean the work surface and walls with an appropriate disinfectant and soapy water afterward.
- Clean the sash window with an appropriate disinfectant and glass cleaner afterward.
- Use a damp cloth to clean the exterior surface of the BSC, particularly on the front and top, to remove dust that has accumulated there.
- Use sterile water to finish the cleaning and wash away any residue of disinfectant, soapy water, and glass cleaner.
- Avoid using bleach to clean the surface.
- For removing stubborn stains or spots on the stainless-steel surface, use stainless steel polisher (Autosol®). In such cases, make sure that you wash the steel surface immediately afterward with sterile water and some liquid detergent. Use a polyurethane cloth or sponge for washing. Regular cleaning of the stainless-steel surface helps retain the attractive factory finish.
- Ensure that the chemicals used are compatible with one another.
- Use appropriate personal protective equipment (PPE) when carrying out the activity.
Overall, biological safety cabinet installation, safety tips, and maintenance are essential for lab safety, experiment reliability, regulatory compliance, cost-efficiency, and emergency preparedness. Be equipped with knowledge whenever you use Biosafety Cabinets and heed the given installation and maintenance guide to let your BSC thrive.
Discover the latest Esco Lifesciences Biosafety Cabinet: Labculture® G4 Class II Type A2 BSC with Centurion Touchscreen Controller
Ready to learn more about Biosafety Cabinets? Reach out to us today!
Read More: Esco Lifesciences BSC Cabinet Services, What are Biosafety Cabinets?