
A Biological Safety Cabinet (BSC), also known as a Biosafety Cabinet is mainly used for handling pathogenic biological samples or for applications that require a sterile work zone. A biological safety cabinet creates inflow and downflow of air that provides operator protection. The downflow air passes through an ULPA/HEPA filter and creates an ISO Class 3 work zone to protect samples from the risk of cross-contamination. The air exhausted also passes through an ULPA/HEPA filter prior to release to protect the environment.
Esco biosafety cabinets have a wide range of options from work trays, side panel construction to accessories. Esco BSCs are designed with ergonomic and energy-saving features.
To guarantee the biological safety cabinet's optimum performance these are tested and classified by 2 standards: EN 12469:2000 and NSF 49.

EN 12469
EN 12469: 2000 Biotechnology - Performance criteria for microbiological safety cabinets is the new harmonized European standard for microbiological safety cabinets, published by CEN, the European Committee for Standardization. This standard classifies BSCs into to Class I, Class II, and Class III.

NSF
The NSF International (formerly The National Sanitation Foundation) Biological Safety Cabinetry Program was initiated during the 1970s at the request of the regulatory community, including the Centers for Disease Control (CDC), National Institutes of Health (NIH), and the National Cancer Institute (NCI). This standard further classifies Class II Biosafety Cabinets according to subtypes based on air circulation: Class II Type A1, Class II Type A2, Class II Type B1, and Class II Type B2.

A Class I Biosafety cabinet protects the operator and the environment from exposure to biohazards. It does not prevent samples being handled in the cabinet from being exposed to contaminants that may be present in room air. Naturally, there is a possibility of cross-contamination that may affect experimental consistency. Consequently, the scope and application of Class I cabinets is limited, and it is largely considered obsolete.

Class II Type A2
The Class II Type A2 biological safety cabinet is the most common Class II cabinet. It has a plenum from which 30% of air is exhausted, and 70% re-circulated to the work area as the downflow.
Stated from NSF/ ANSI 49:2010, both the Class II Type A1 and Type A2 must have the positively-pressurized contaminated plenum to be surrounded by negative pressure. In case there is a leakage on the positive plenum, the leaking aerosol will be pulled by the negative pressure back to the positive plenum, and it will not leak out.
In the A2 cabinet, about 70% of air from the positive plenum is recirculated as downflow, and the remaining 30% is discharged to the lab through the exhaust filter.
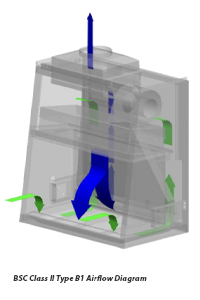
Class II Type B1
The Class II Type B1 biological safety cabinet has a common plenum from which 70% of air is exhausted, and 30% re-circulated to the work area as the downflow. This cabinet also has a dedicated exhaust feature that eliminates re-circulation when work is performed towards the back within the interior of the cabinet. Toxic chemicals employed as an adjunct to microbiological processes should only be allowed if they do not interfere with work when re-circulated in the downflow.

Class II Type B2
The Class II Type B2 biosafety cabinets are suitable for work with toxic chemicals employed as an adjunct to microbiological processes under all circumstances since no re-circulation occurs. In theory, Type B2 biological safety cabinets may be considered as the safest of all Class II BSCs since the total exhaust feature acts as a fail-safe in the event that the downflow and / or exhaust HEPA filtration systems cease to function normally. However, Class II Type B2 biosafety cabinets require large laboratory spaces due to their installation system and will require elaborate ducting works.
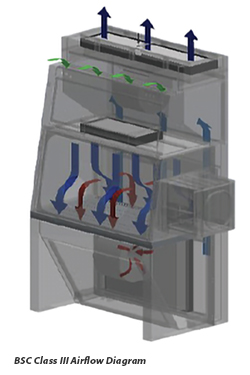
Class III biological safety cabinets are suitable for work with microbiological agents assigned to biosafety levels 1, 2, 3 and 4. They are frequently specified for work involving the most lethal biological hazards.
Work is performed through glove ports in the front of the cabinet. During routine operation, negative pressure relative to the ambient environment is maintained within the biosafety cabinet. This provides an additional fail-safe mechanism in case physical containment is compromised. Exhaust air is usually HEPA filtered and incinerated. Alternatively, double HEPA filtration with two filters in series may be utilized.
Risk Groups are classifications that describe the relative hazard posed by infectious agents or toxins in the laboratory.
The World Health Organization (WHO) defines the risk groups as:
- WHO Risk Group 1- no or low individual and community risk
- WHO Risk Group 2- moderate individual risk, low community risk
- WHO Risk Group 3- high individual risk, low community risk
- WHO Risk Group 4- high individual and community risk